As part of the Company’s current slate of low capital intensity, high-return incremental growth investments, Dow announced it will retrofit proprietary fluidized catalytic dehydrogenation (FCDh) technology into one of its mixed-feed crackers in Plaquemine, Louisiana, to produce on-purpose propylene. The retrofit will enable Dow to continue to meet growing demand for its businesses serving consumer, infrastructure and packaging end-markets, while also remaining within its stated near-term capital expenditure targets.
In 2016, Dow expanded the ethylene capacity of this same cracker by more than 225,000 metric tons and added the ability to crack ethane, while maintaining the flexibility to crack propane, butane and naphtha.
Dow and other U.S. cracker operators are consuming more ethane instead of heavier feed slates, resulting in a reduction of coproduct production, including propylene. This reduction in propylene has created a supply/demand gap in the U.S. that requires additional on-purpose propylene sources to meet the needs of downstream derivatives.
The FCDh technology retrofit further improves Dow’s ability to continue to source the most advantaged feedstocks, while also producing reliable and cost-efficient on-purpose propylene to supply its integrated derivative units in Louisiana. The technology can also reduce capital outlay by up to 25 percent and lower energy usage and greenhouse gas emissions by up to 20 percent, thereby improving overall sustainability when compared to conventional propane dehydrogenation technologies.
The retrofit will enable production of more than 100,000 metric tons of additional on-purpose propylene at full run-rate, further back-integrating Dow’s derivative facilities to cost-advantaged propylene while also maintaining the unit’s current ethylene production capacity. The project is expected to begin producing on-purpose propylene by the end of 2021.
“Deploying FCDh technology supports Dow’s continued focus on delivering low-risk, low-cost and high-return projects while reducing the energy intensity and carbon footprint associated with conventional technologies,” said Keith Cleason, vice president of Dow’s Olefins, Aromatics & Alternatives business. “Retrofitting our Plaquemine cracker will enhance asset utilization and leverage the U.S. shale gas advantage to meet growing customer demand for Dow’s differentiated polyolefins products.”
Dow’s licensable FCDh technology won R&D100 and ICIS Process Technology Innovation awards in 2017. It is one of the most economical propane dehydrogenation (PDH) technologies available today. It can be used to construct a stand-alone PDH facility or can be integrated with existing crackers to provide ‘plug and play’ capabilities for a variety of plant configurations.
In July, PetroLogistics ll LLC announced it had licensed Dow’s proprietary FCDh technology for a new stand-alone PDH facility it plans to construct on the U.S. Gulf Coast.
“Adaptable FCDh technology demonstrates the combined power of Dow’s innovation and integration to create breakthrough solutions,” said A.N. Sreeram, senior vice president, Research & Development, and chief technology officer for Dow. “Dow’s advanced FCDh technology is flexible, scalable, reliable and more sustainable, allowing for use in multiple configurations in a range of capacities – stand alone or integrated into crackers.”
Source: Dow Chemical
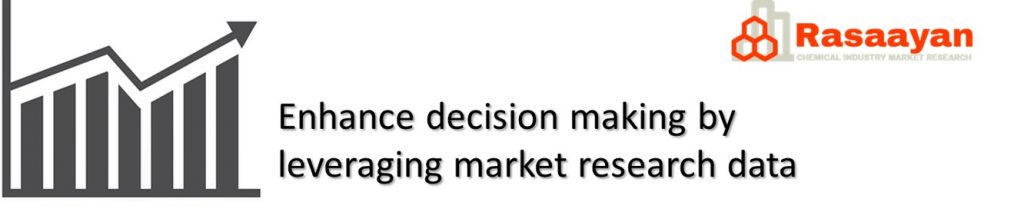